Sustainability and historic buildings
Assessing the energy rating of a historic building needs to take into account the energy required to build it in the first place, argues historic building consultant Alan Tierney
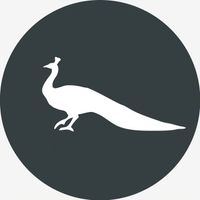
As mentioned in my last blog, historic buildings come out very badly in energy assessments - largely because of flawed assumptions and a lack of accurate data.
That's not even half the story, though. The really big problem with energy assessments is that they only take account of energy "in use" - basically what is needed for heating and lighting. No account is taken of the energy required to put the building up in the first place: its embodied energy (EE).
The EE of a building is the total energy required to construct it - to obtain the raw materials, process and manufacture them as necessary, transport them to site and put them together.
This is a major factor in the energy profile of a building. Estimates of quite how major vary widely. One report reckoned that the EE in the construction of an Edinburgh tenement was equivalent to 1000 years of its energy for power and heating. It's more usual to regard the pay-back period at 50-100 years but, paradoxically, the more energy efficient the building the longer it is!
Historic buildings have very low EE compared with their modern counterparts. This is for a number of reasons:
Old buildings tended to be constructed from natural materials. Where they were processed (e.g. bricks and clay tiles) this was done in a less energy intensive manner than in today's industrialised world. For example, the EE in production of concrete is about 7 times that of rammed earth (e.g. cob or witchert) and modern bricks nearly 3 times traditional clay bricks and 27 times limestone.
Then transport adds greatly to the EE of today's construction materials. They tend to be bulky and are often carried huge distances to site, doubling the EE of buildings. In contrast, materials for older buildings were sourced locally and transported very short distances - typically no more than 5 miles before the arrival of canals.
Exquisite houses, the beauty of Nature, and how to get the most from your life, straight to your inbox.
Many old buildings incorporate large quantities of plant based material: timber, straw, hemp etc. These absorbed CO2 when they were growing, before being permanently incorporated into the building. This locks up that carbon - referred to as sequestered carbon.
Historically, labour costs were low compared to the value of materials. As a result, durability of materials was a prime concern; time and craftsmanship was expended in an essentially manual process. This is reversed in modern construction, where highly manufactured materials are put together by energy-intensive, mechanised processes to minimise the cost of labour.
New build houses are energy intenstive to construct
Historic buildings are, of course, old; they have long ago repaid their energy debt and sequestered carbon is still locked up. They are durable - few buildings constructed today will still be standing in 500, or even 150, years. Their durable materials need regular maintenance rather than frequent replacement.
This brings us to an extreme contrast between old and new: windows. I previously highlighted the English Heritage findings that single glazed, softwood windows can perform as well as modern uPVC units. But what about the EE?
The EE of uPVC is a whopping 13 times that of softwood. While a well maintained softwood window will last indefinitely, the typical lifespan of a uPVC unit is 10-15 years. If the glass is broken in a timber window, it is reglazed; a broken pane in a uPVC window means total replacement. Replacement cycles increase the EE of uPVC over the lifetime of a building by a factor of 10!
The closer you look, the more the gap between old and new widens. Historic buildings change hands much less frequently than modern buildings and new owners make fewer, less extensive changes to old buildings than to modern ones. This is partly because of listed building controls but also the inherent durability and value of the older components. The high rate of churn and refurbishment of many modern buildings will mean their embodied energy exceeds operational energy over their lifecycle.
So what does all this mean? Well, as American architect Carl Elefante put it, "the greenest building is the one that's already built." In other words, careful and sensitive upgrading of existing buildings is much more sustainable than replacing them. What is more, because historic buildings are so far ahead of modern buildings in embodied energy, they shouldn't need to meet the same exacting standards for energy-in-use to justify their sustainability.
Alan Tierney is a historic building consultant. He runs Picketts Historic Building Conservation, advising clients on all aspects of the care, maintenance and alteration of historic buildings. This includes working with homeowners to improve energy performance by sustainable means, while protecting the integrity and value of our precious resource of old buildings.
Picketts Conservation is a member of ProjectBook, which has been created to help owners of listed or period properties understand how their buildings work and to help them find appropriate craftsmen, products and specialist information. The online Heritage Register contains over 540 registered businesses, the largest directory of its type in the UK. For more information, visit www.projectbook.co.uk
Country Life is unlike any other magazine: the only glossy weekly on the newsstand and the only magazine that has been guest-edited by HRH The King not once, but twice. It is a celebration of modern rural life and all its diverse joys and pleasures — that was first published in Queen Victoria's Diamond Jubilee year. Our eclectic mixture of witty and informative content — from the most up-to-date property news and commentary and a coveted glimpse inside some of the UK's best houses and gardens, to gardening, the arts and interior design, written by experts in their field — still cannot be found in print or online, anywhere else.
-
The life that thrives among the dead: How wildlife finds a home in the graveyards and churchyards of Britain
Home to a veritable ‘Noah’s Ark of species’, thanks to never being ploughed, sprayed or fertilised, our churchyards offer a sacred haven for flora and fauna, says Laura Parker.
-
‘What a shame when a dinosaur disappears into the mansion of an oligarch rather than being displayed for all to enjoy’: The ethics of the dinosaur auction
Fancy a stegosaurus in your living room? You can buy one at auction. But the latest luxury good is a paleontologist's worst nightmare.