The artisans helping the British ceramics industry thrive into the 21st century
Reports of the death of the British ceramics industry are premature, says Giles Kime.
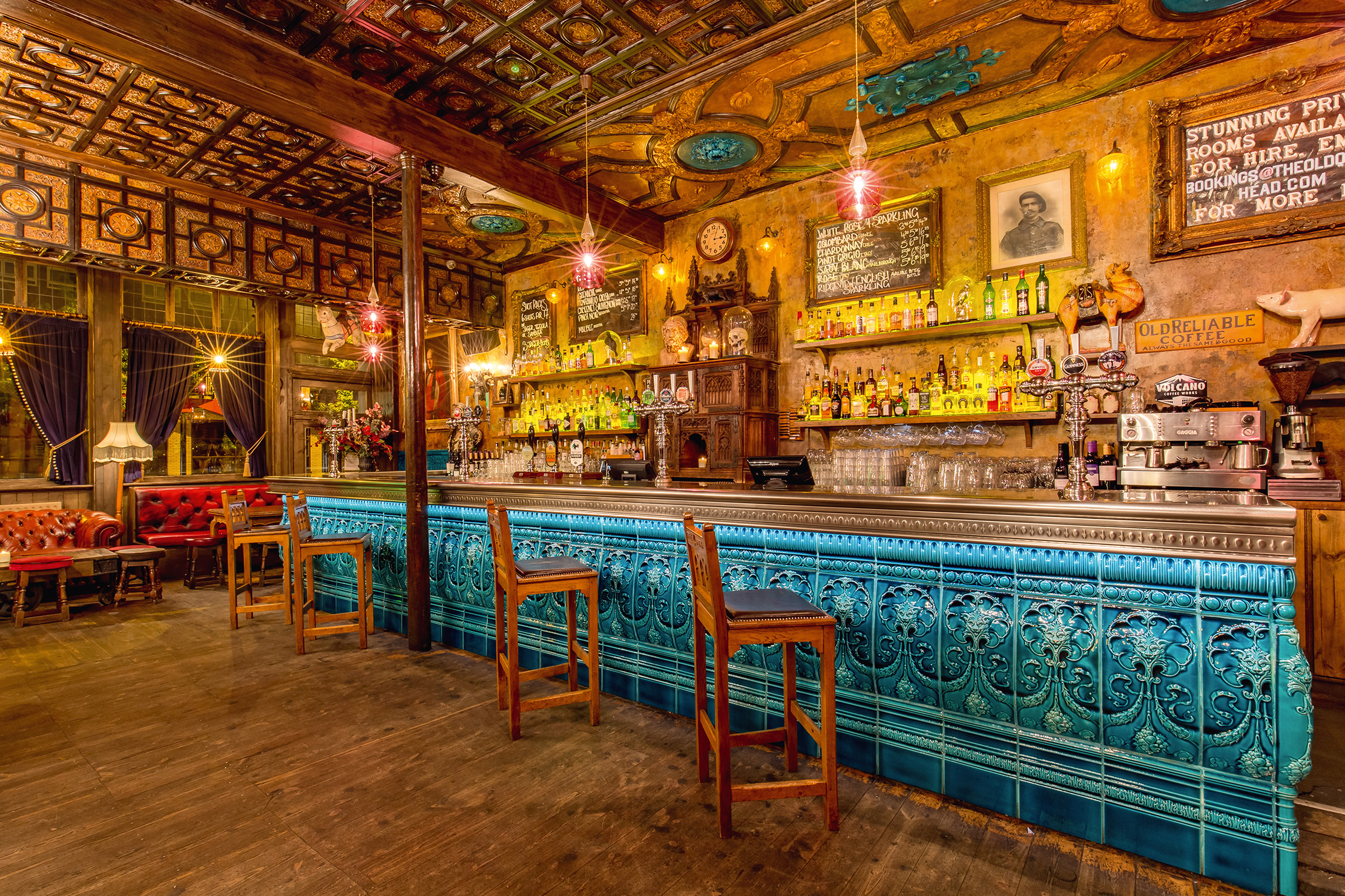
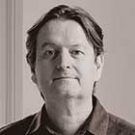
Although there’s a lot of talk of supply-chain issues, some building materials are closer to hand than is ever acknowledged. Anyone who has ever observed the inner workings of a building made before the 19th century will be aware that the key ingredients had rarely travelled far. Medieval builders used whatever came to hand; soil, sand, animal dung, straw, twigs and strips of wood; bricks were often made on site from local clay. It’s the use of such materials — wattle and daub across Britain, oolitic limestone in the Cotswolds, granite in Scotland — that lend the regions their distinctive flavours.
British soil is a more productive source of building materials than many people realise. Recently, stone specialist Artorius Faber has done a brilliant job of highlighting the treasures beneath our feet. Last year, Chesney’s launched a range of fire surrounds made from stone sourced by Britannicus Stone from British quarries, such as Blue Ball Eye from Derbyshire, Swaledale Fossil from North Yorkshire and glorious red Stoneycombe from Devon.
There has always been a symbiotic relationship between the availability of materials and architectural styles. It was the dearth of good-quality timber that precipitated the widespread use of brick in the 17th century and the availability of steel and float glass, plus, eventually, synthetics, that transformed buildings in the succeeding centuries.
In the 1800s, the growth of the ceramics industry saw its widespread use in architecture (think the exteriors of the Royal Albert Hall, Harrods and the Natural History Museum). Availability has long been the mother of invention; when Arthur Shaw saw the possibilities of the fireclay unearthed at the colliery he inherited in Lancashire, he created Shaws of Darwen, which provided the tiles for the Wrigley Building that rose above the Chicago skyline in the 1920s. Today, Shaws is famous the world over for the Belfast sinks that are still made in Darwen.
It’s not only a desire for materials with a small carbon foot- print that is driving the popularity of British ceramics, it’s a mix of both craftsmanship and quality. Shaw’s sinks are finished by hand and glazed twice, processes that achieve a superlative look and feel.
It is quality that is the attraction of time-honoured ceramics business Craven Dunnill Jackfield, established in Ironbridge, Shropshire, in 1872 by architect Charles Lynam, who specialised in industrial buildings. Characterised by rich glazes, decoration and encaustic designs, they add depth to an interior, from Victorian to moodily contemporary. Recently, the company collaborated on a range with Burleigh of Burslem, another 19th-century cera-mics business thriving in the 21st.
Best joiners, plasterers, kitchen designers and craftspeople in Britain, in the Country Life Bespoke Bible
Country Life names Britain's top bespoke craftspeople, extraordinary practitioners from joiners and stonemasons to furniture-makers and metalworkers.
Exquisite houses, the beauty of Nature, and how to get the most from your life, straight to your inbox.
The experts from R Moulding & Co on how good-quality, well-chosen materials make for beautiful buildings
Moulding of traditional builders R. Moulding & Co explains the relationship between good-quality, well-chosen materials and beautiful buildings.
Plasterwork perfection contained within an unassuming Devon farmhouse
The ornate plasterwork of the 17th century reached a high-point in the West Country, as Roger White discovers at the
-
The pinnacle of the English style of gardening, as fine today as it was a century ago
Charles Quest-Ritson has just returned to Great Dixter for the first time in years — and it's 'the high point of all my garden visiting for a long time. I cannot recommend it too highly'.
-
How the acrobatic buzzard survived persecution to become one of Britain's best avian hunters
It may appear lethargic, but no one could argue with the hunting prowess of the common buzzard when it transforms into a surging missile intent on an unsuspecting victim.