Dream house - Chimneypiece maker
Mary Miers meets a chimneypiece maker based in Scotland who makes historic copies from pine which can be adapted to suit individual specifications.
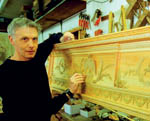
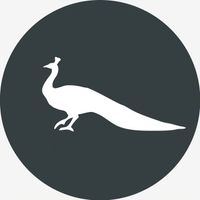
The 'Adam chimneypiece' is an icon of neo-Classical taste that is still popular today. Yet the history of how they were mass produced in 'pine and gesso' is not widely known. Fine chimneypieces were generally carved out of marble or lime wood, until growing demand during the Georgian building boom began to outpace supply, exacerbated by the embargo on importing marble during the Napoleonic Wars. So the Adam practice pioneered the production of a cheaper, less labour intensive alternative, made of pine and what was known as 'Adam's composition' a putty-like substance mixed to a secret recipe that William Adam claimed he got from a Swedish philosopher, which could be cast from moulds to create decorative ornament then applied to timber frames. These chimneypieces were exported abroad, often as ballast in ships returning empty from Glasgow or Leith. Soon, they were being widely copied on the east coast of America, where their distinctly Scottish interpretation of Classical detail spare and concise by comparison with the heavier ornamentation of their English counterparts manufactured by firms such as Wolstenholmes of York became as much a symbol of the American Federal style as it was of Adam neo-Classicism. Today, there are plenty of cheap 'repro' chimneypieces on the market (many made in China), but one company has revived the authentic composition recipe and is producing high-quality facsimiles of the Adam originals, using the traditional method. In an echo of history, Thistle & Rose was founded to meet a supply problem this time resulting from the growing fashion for restoring old houses and reinstating fittings of decent quality. The catalyst was a visit made in 1990 by the company's co-founder, David Black, to Sir Henry Raeburn's house, where he was horrified to discover that all the chimneypieces had been stolen. 'I felt it was an appalling loss of Edinburgh's heritage, but nobody seemed bothered. Thefts were rife in the New Town, and I thought that if affordable, good-quality copies were available, the problem could be reduced.' So, after an abortive attempt by the Edinburgh New Town Conservation Committee, 'I decided to produce them myself'. Coincidentally, the cabinetmaker Kim Roberts, who was working for Mr Black, said he had always wanted to try making one, 'so I gave him an original I was about to install and told him to see what he could do. After researching and adopting the original recipe, he came up with a beautiful copy'. They established their 'atelier business' in Hawick in the mid 1990s, and Mr Roberts now works here with four other craftsmen. They make the frames from Scots pine, each tree carefully sourced, sawn locally and traditionally seasoned. Moulds are made by taking casts from original details. 'You have to get to know your mould. Each one requires different handling, and it's a knack pressing in the warm putty a mix of chalk, animal gelatine, water, linseed oil and rosin.' It is ready to be removed after a few minutes, when it is cut off its backing and put into a fridge. When all the details are ready, they are trimmed, and then stuck onto the sealed and sanded frame. The consistency of the compo is similar to Cheddar cheese, but, after some days, it becomes brick hard. If painting is required, chimneypieces are sprayed in the workshop and then touched up by brush; other finishes include marbling, glazing and gilding. Thistle & Rose manufactures 12 designs copied from historic examples, which can be adapted to suit individual specifications; each costs about £2,000. They also make one-off facsimiles, and restore and clean originals. Mr Roberts has another business too, Chisholm Antiques, which makes and restores furniture and carves chimneypieces in lime wood and mahogany. Thistle & Rose 01450 376928; www.thistleandrose.net Top tips
Use only a damp cloth to clean; water discolours and damages gesso18th-century composition pieces were nearly always painted to protect the gessoNever use wire wool to remove old paint. Use special tools and controlled chemicals, and, ideally, a professional
Exquisite houses, the beauty of Nature, and how to get the most from your life, straight to your inbox.
Country Life is unlike any other magazine: the only glossy weekly on the newsstand and the only magazine that has been guest-edited by His Majesty The King not once, but twice. It is a celebration of modern rural life and all its diverse joys and pleasures — that was first published in Queen Victoria's Diamond Jubilee year. Our eclectic mixture of witty and informative content — from the most up-to-date property news and commentary and a coveted glimpse inside some of the UK's best houses and gardens, to gardening, the arts and interior design, written by experts in their field — still cannot be found in print or online, anywhere else.
-
Bank holidays, big churches and which country has the most timezones? Country Life's Quiz of the Day, August 22, 2025
Head into the bank holiday weekend bursting with knowledge after Friday's Quiz of the Day.
By Country Life Published
-
‘Some people find it a bit daunting being faced with a big beast and a couple of utensils’: Mitch Tonks on the perfect seafood platter
Mitch Tonks creates the ultimate fisherman’s feast using crab, langoustines and of course, oysters.
By Will Hosie Published
-
How to prepare your house for winter
As winter approaches, experts advise that preventative measures are crucial for our houses to weather hard winters
By Country Life Published
-
Ten house tips for the winter
Now is the time to put your house in ship-shape for the winter months ahead. Chartered surveyor Tom Grillo shares his ten top tips
By Country Life Published
-
Choosing an interior designer
Finding the right skilled interior designer for your period property requires some dedication; in particular you need to make sure you share the same vision
By Country Life Published
-
Maintenance tips for Victorian houses
There are a number of aspects to look out for when viewing or indeed owning a Victorian house
By Country Life Published
-
Best cooking pans
Mrs Danvers suggests the best makes of pots and cooking pans to hunt down when shopping for a special friend's wedding present
By Country Life Published
-
How to save old floorboards
Lots of care and elbow grease can help old floorboards gleam again
By Country Life Published
-
Buying bellows
Mrs Danvers recommends where to find a new or antique pair of bellows
By Country Life Published
-
Removing chocolate stains
Mrs Danvers tackles readers' household queries: this week's are chocolate stains on a linen suit and screen doors
By Country Life Published