Dream house: lime-mortar worker
Mary Miers meets a lime-mortar worker who is an expert in his field...
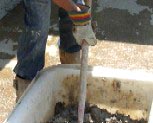
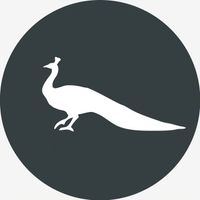
Over the years, many buildings have been stripped of their render in the mistaken belief that exposed masonry is historically authentic. Yet in the past, most buildings were covered with a protective coat of plaster to deter the damaging effects of wind, rain and frost. 'What's now regarded as complicated was a simple, elementary building practice that could be done by all. It required some attention to detail and a good understanding of how buildings performed and looked,' says builder Tim Meek, a Yorkshireman who has been working with lime since the 1980s. He remembers being on a field trip to Prudoe Castle, where he noticed that those undertaking conservation work were 'working in a very different way to what had been done there in the past. I started looking very closely at the materials and the craftsmanship of lime and noticed how careful the work was. All I've done is copy it. Very few others were doing this at the time'. Now based in Scotland, Mr Meek has worked all over Britain and as far afield as America and the Caribbean. Unlike Portland cement, which became popular from the 1830s because of its fast drying time and effectiveness under water, lime mortar doesn't become stiff and brittle; it allows some movement, and is permeable, enabling buildings to breathe. It is also very Green, not only in the way it is produced, but also because it reabsorbs CO2 from the atmosphere. 'It therefore sits nicely in both the worlds of building conservation and environmentally friendly new architecture.' He adds that 'aesthetically, there is simply no substitute'. He makes his own lime putty, adding water to calcium oxide (quick lime) and leaving it to slake for months to produce calcium hydroxide (lime putty). He then mixes in sand and sometimes hair for extra strength to produce a mortar which can be used to bed stones or bricks, or for plastering walls. For roughcast renders, coarser aggregates (grit or shells) are added, which increase the surface area, thereby maximising water evaporation. This is the norm in wet areas, such as Scotland, where it is known as 'harling' because the plaster is thrown or 'hurled' onto the surface rather than trowelled. 'Lime plaster should be used sparingly and economically,' says Mr Meek. First, the wall surface and joints are 'packed out' with small pieces of tile, stone and brick embedded in mortar and left for about a week. Then, one or two coats of render are applied. Regular spraying with water is an important part of the process, as is keeping the wall covered with a tarpaulin. For internal walls and ceilings, the technique is broadly similar, although drying may take longer, and a third, more refined coat may be applied. With modern plasterboard partitions, which lack texture and natural irregularities, it is possible to create the appearance of lime plasterwork (although it will not be permeable) by mixing lime and sand with polyvinyl acetate, skimming it on, and, once it has firmed up, running in a coat of fine, sandy limewash, and then limewashing on top. Limewash is a liquid mix of lime putty, water and pigments which, applied liberally in three or four coats, provides a protective, permeable and beautifully coloured finish. It is cheap and easy to apply, and, being alkaline, has good sterilising properties. Mixed with earth pigments, it produces a range of gorgeous earth colours that weather beautifully and have a luminosity and patina unrivalled by paint. Tim Meek 01381 610446 Top tips Traditionally, most buildings were protected by a lime render and limewash Moisture content in the air can create variations in the pigmentation of limewash?this is part of its visual character Using lime is more labour intensive, and therefore more expensive, unless you do it yourself, which is easy and satisfying
Exquisite houses, the beauty of Nature, and how to get the most from your life, straight to your inbox.
Country Life is unlike any other magazine: the only glossy weekly on the newsstand and the only magazine that has been guest-edited by His Majesty The King not once, but twice. It is a celebration of modern rural life and all its diverse joys and pleasures — that was first published in Queen Victoria's Diamond Jubilee year. Our eclectic mixture of witty and informative content — from the most up-to-date property news and commentary and a coveted glimpse inside some of the UK's best houses and gardens, to gardening, the arts and interior design, written by experts in their field — still cannot be found in print or online, anywhere else.
-
'One of the finest houses in Cheshire' blends Georgian architecture, modern exoticism and space to park your helicopter
Penny Churchill looks inside Stretton Hall, an exceptional house for sale
By Penny Churchill Published
-
Marilyn, maraschino cherries and classic movie musicals await you in Country Life's Quiz of the Day, August 29, 2025
Friday's quiz puts your cocktail knowledge to the test.
By Country Life Published
-
How to prepare your house for winter
As winter approaches, experts advise that preventative measures are crucial for our houses to weather hard winters
By Country Life Published
-
Ten house tips for the winter
Now is the time to put your house in ship-shape for the winter months ahead. Chartered surveyor Tom Grillo shares his ten top tips
By Country Life Published
-
Choosing an interior designer
Finding the right skilled interior designer for your period property requires some dedication; in particular you need to make sure you share the same vision
By Country Life Published
-
Maintenance tips for Victorian houses
There are a number of aspects to look out for when viewing or indeed owning a Victorian house
By Country Life Published
-
Best cooking pans
Mrs Danvers suggests the best makes of pots and cooking pans to hunt down when shopping for a special friend's wedding present
By Country Life Published
-
How to save old floorboards
Lots of care and elbow grease can help old floorboards gleam again
By Country Life Published
-
Buying bellows
Mrs Danvers recommends where to find a new or antique pair of bellows
By Country Life Published
-
Removing chocolate stains
Mrs Danvers tackles readers' household queries: this week's are chocolate stains on a linen suit and screen doors
By Country Life Published